The demands for sustainability, safety, and cost-effectiveness are ever-growing in professional kitchens truly investing in customer experience. Kiilto’s experts answered the challenge faced by Viking Glory and created an innovative centralized dispensing system for the cruise ship’s restaurants, saving not only water, materials, and space but also the valuable time of its users.
Climate-wisdom is created through impactful choices
Viking Glory, sailing through the postcard-like scenery of the Baltic Sea archipelago, is a flagship for a modern, more responsible era of cruise tourism. One of the world’s most climate-wise passenger ships offers its passengers a unique setting for experiential seafaring, without compromising on sustainability and safety – or the lavish dining experiences cruise ships are known and loved for.
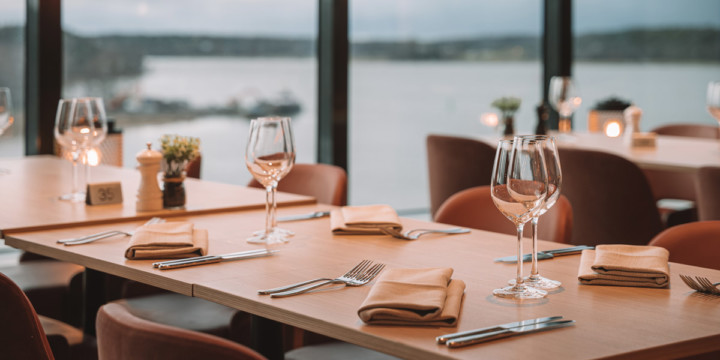
Having made significant investments in technical solutions that reduce the environmental impact of cruise tourism, the designers of Viking Glory were looking for additional momentum from innovations to support the numerous restaurants on the ship. By streamlining and securing processes, the aim was to provide the restaurant professionals on board with effective tools for working as safely and effortlessly as possible, reducing both the workload and the environmental impact.
A safer and more efficient future for professional kitchens
Kiilto’s professional hygiene experts accepted the thrilling challenge and developed a dosing system tailored to the needs of Viking Glory, enabling a centralized and automated feeding of detergents and rinse aids into the machines in its kitchens. Saving working hours and square meters, the dispensing center makes room for what’s most important: creating memorable moments of indulgence and taking care of the passengers’ comfort.
“Kiilto has been a trusted partner of Viking Line for years now – our experts also created a similar system on Viking Grace no less than ten years ago,” says Kiilto’s hygiene expert and Key Account Manager, Mika Sipponen. “The safety and well-being of the staff was a central starting point then and now: the centralized system allows the crew not to be involved with chemicals on a daily basis.”
According to Sipponen, the innovative system offers its users not only safer and healthier working conditions but also an effortless user experience for decades to come.
The distribution center is located on the ship’s auto deck, from which the necessary cleaning agents are transferred through pipes to the ship’s washing machines
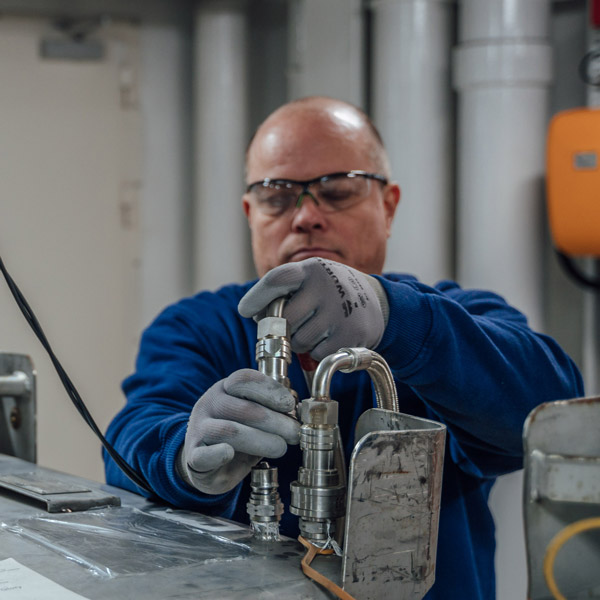
Kiilto’s technical expert Mikael Vuorinen has supported Viking Glory’s crew during and after the introduction of the dosing system.
“The reliability and maintenance security of the equipment is undoubtedly particularly important on ships, as malfunctions rarely occur conveniently when the ship is anchored in port. The dispensing system on the Viking Glory has been doubled to ensure continuous operation in case of equipment failure. In addition, the technical experts of Kiilto are always on hand to support the crew, both on land and at sea.”
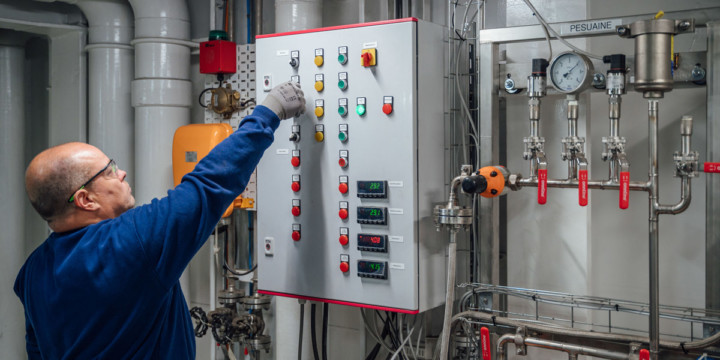
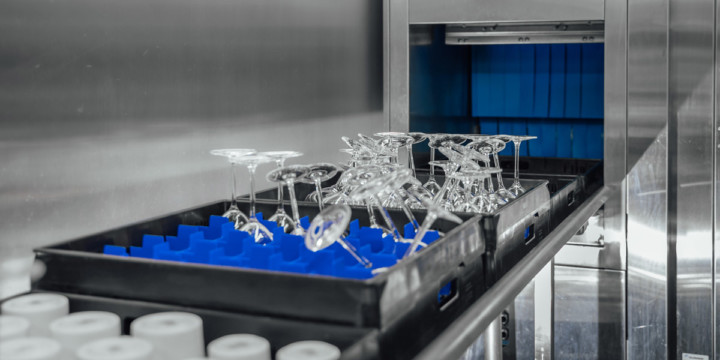
Centralized dispensing system creates comfort – as well as savings
Developed through close collaboration with the designers of the Viking Glory, the innovative dispensing system was installed on the ship’s auto deck. From there, it automatically dispenses detergent and rinse aid to the fifteen dishwashers situated in the vessel’s many restaurants. This fully automated system streamlines the workload in the hectic kitchens, where dishes can now be simply loaded into the washing machines, and the system takes care of the rest – guaranteeing a consistently high-quality outcome.
The user-friendly equipment optimizes detergent dispensing, bringing significant savings in both water consumption and transportation costs, as well as reducing the amount of waste and chemical load on the environment. The staff avoids direct contact with chemicals, which effectively supports workplace safety.
“The similar system implemented by Kiilto onboard Viking Grace has been proven to be not only functional and safe, but also extremely effective in challenging conditions over the past decade,” elaborates dispensing system expert Juha Lipponen. “For the Glory dosing unit, we utilized the lessons learned from the previous system and made the necessary component replacements to ensure spare part management and availability in both systems.”
In addition to safety, Lipponen sees the ease of use and maintenance freedom as an advantage of the centralized dispensing system.
“It truly benefits the staff and their safety that all chemicals are centralized and controlled in one place, and not, for example, in the kitchens. The system is also largely maintenance-free – the pumps are of course maintained regularly, but there are very few wear and tear parts in the equipment.”
Kitchen experts endorse the innovative dispensing system with enthusiasm
So, what does the everyday life of Viking Glory’s kitchens look like now that the dispensing system has been in active use for almost a year? Kitchen manager Mikko Martikainen is thrilled with the concrete benefits and ease brought by the centralized set-up:
“The dispensing system has been working great and it significantly eases the daily work of the restaurant staff. Such a vast amount of dishware passes through the machines daily that without a centralized structure we would constantly have to change detergent containers – and repeatedly come in contact with chemicals. The system also frees up storage and workspace as the machines and detergent containers are located on the auto deck.”
The centralized dispensing set-up has significantly eased the daily routines in Viking Glory’s kitchens.
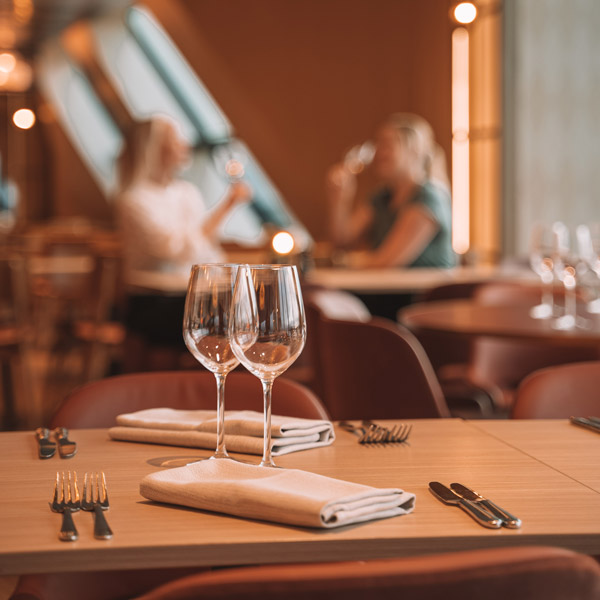
The dosing system makes room for what matters most: creating memorable encounters and experiences for the passengers.
Kiilto is a partner that promises to stay by the customer’s side all the way, from design to maintenance. Martikainen agrees:
“We all know that challenges can sometimes arise, and it doesn’t always happen while the ship is in port: we might also need help at sea to keep operations running. Kiilto’s technical expert Mikael Vuorinen has been very hands-on in instructing and guiding our staff, making sure everyone knows how the system works. And if we have any questions or concerns, we get prompt advice either by email or phone – and also a maintenance visit to the ship when needed. Cooperation with Kiilto has gone smoothly and we are more than pleased with the service we’ve received!”
Kiilto’s centralized dispensing system for machine dishwashing
- Enables centralized dispensing of detergents to multiple separate dishwashers automatically, without manual operation
- Excellent for serving the daily operations and customer experience of professional kitchens, hotels, and shopping centers
- Safe and nearly maintenance-free
- Supports sustainability by optimizing chemical usage and water consumption
- Saves working hours and space
In co-operation with: Viking Line Text: Mira Ahola Images: Joonas Kortelainen and Mikko Uosukainen